The use of ceramics in watches represents a modern marvel of material science, becoming a trendsetter since its introduction to consumers in the last century. In 1962, Swiss Rado introduced the world’s first watch featuring ceramic components, the ‘Rado DiaStar.’ Although its case was made from tungsten carbide rather than being entirely ceramic, the limited use of ceramic material in the ‘Rado DiaStar’ laid the groundwork for the subsequent flourish of diverse ceramic watches.
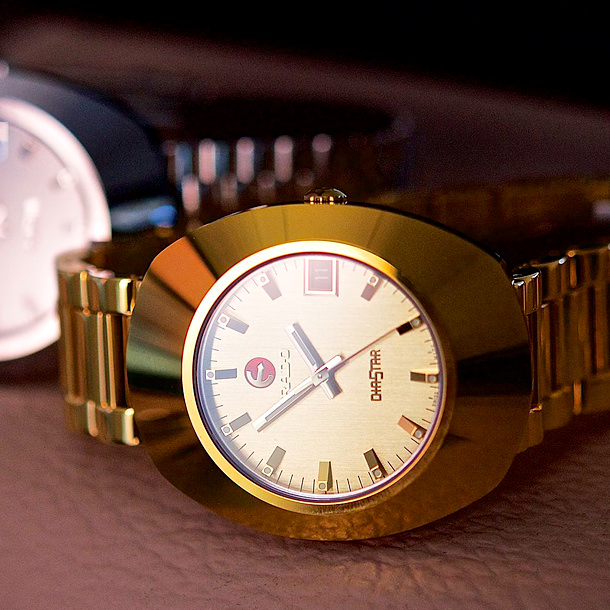
If the ‘Rado DiaStar’ was a cautious experiment in using ceramics for watches, then the ‘Omega Seamaster Cermet AKA Black Tulip Case’ launched by Omega in 1972 represented a bold venture in utilizing ceramics for watch cases. Unfortunately, the ‘Omega Seamaster Cermet AKA Black Tulip Case’ was produced in very limited quantities and eventually left the market as swiftly as it had appeared.

In 1986, a groundbreaking ceramic case watch emerged: the luxury ‘Da Vinci Perpetual Calendar Chronograph 3755’ produced by IWC. This watch daringly utilized high-tech ceramics made from zirconium oxide, known for their high hardness and the ceramic’s natural luster, which quickly led to its acceptance in the luxury market.
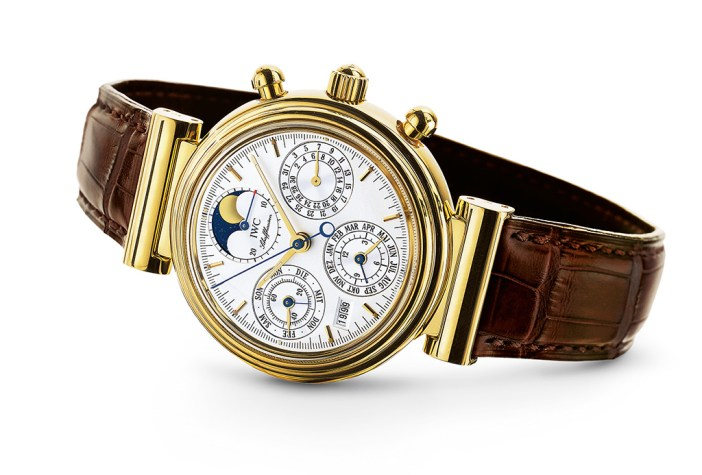
The commercial success of the “Da Vinci Perpetual Calendar Chronograph 3755” made consumers re-evaluate the ancient luxury of ceramics, which retained a mysterious allure in the new era. The ceramic case’s characteristics – its smooth surface, wear resistance, physical stability, acid and alkali resistance, corrosion resistance, resistance to discoloration, light weight, and non-toxicity – made it popular among consumers. Importantly, unlike stainless steel cases and bands that inevitably contain nickel which can irritate the skin, ceramic is more skin-friendly, leading to greater market acceptance.
Realizing the market potential of ceramic cases, major brands like Omega, IWC, Blancpain, and Panerai started to engage in this area. The growth in demand for ceramic cases spurred significant advancements in the required compounds and manufacturing technologies. The current mainstream process for making ceramic cases involves injecting extremely fine zirconium oxide powder into a mold under high pressure, then melting and solidifying it in a kiln at temperatures above 1,000 degrees Celsius to form durable ceramic components. However, the process doesn’t end there. A qualified ceramic case, after sintering, is further polished with diamond powder to complete the small but significant ceramic exterior of the watch.
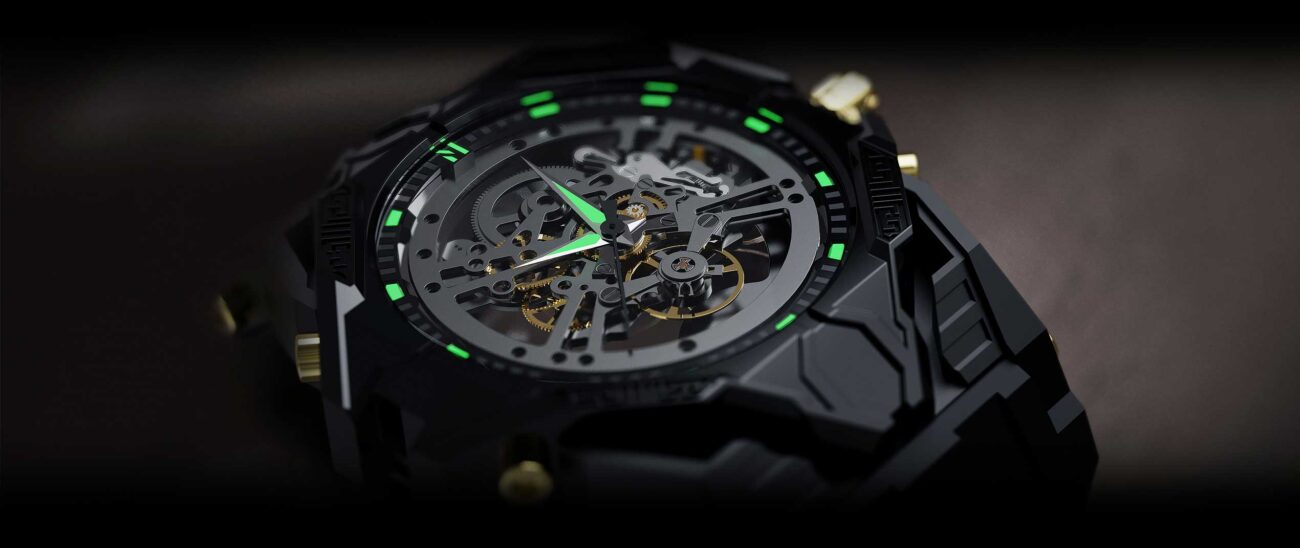